City Tech
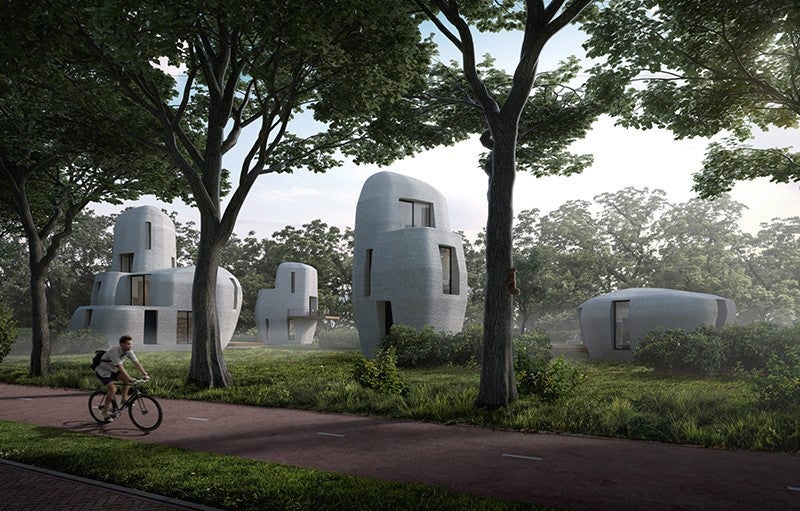
Over the past decade, three-dimensional printing has been one of the buzziest ideas in technology. Instead of adding ink to paper, a 3D printer translates a digital design into an object by adding layer upon layer of material (plastic, metal, concrete) through a computer-guided extruder—almost like a motorized toothpaste tube. More correctly but blandly described as “additive manufacturing,” the process has evolved from rapid-prototyping uses by tech corporations and design firms to widespread experimentation by hobbyists and hackers and startups, making objects from consumer products to toys.
But what about something bigger—like a house?
Actually, researchers and entrepreneurs around the world have been applying variations on the technique to increasingly ambitious building-sized projects for several years. The latest example involves a five-house development in Eindhoven, the Netherlands. It’s an ambitious experiment involving multiple partners that will wrestle with not only the practicalities of design and construction, but also regulation and the real-world marketplace, given that the properties are rentals. “We need a big revolution in the building industry,” said Rudy van Gurp, the project manager for building contractor Van Wijnen Rosmalen, and the application of 3D-printing techniques could be part of that.
The advantages to this still-evolving form of building include more efficient use of materials, which both cuts costs and minimizes waste; speed of construction; and potential for customization. Or at least that’s the promise, if the technology continues to improve at its current pace. That’s one reason the Eindhoven experiment is notable, as it follows a recent burst of related prototyping breakthroughs.
This past March, a firm called Icon in Austin, Texas, used its take on 3D-printing technology to build a sleek, intentionally minimalist 350-square-foot home for a reported $10,000, predicting it could knock the cost down to $4,000 as it modifies its design to further reduce non-“printed” elements. The structure was built to meet local housing codes and is currently being used as a model home and office. Envisioning the process as a potential solution to housing needs in the developing world, Icon is working with the nonprofit New Story to bring its approach to El Salvador.
And in July, a French family of five was chosen to be apparently the first in the world to actually move into a 3D-printed house: a detached, 1,000-square-foot social housing unit with eye-catching curves. The organizers of that project say it cost about $200,000, which they say is 20 percent less than an identical version built using traditional methods. The structure took 54 hours to print—although it took another four months to finish non-printed elements such as the windows and roof.
Both build time and cost are projected to fall as the process is refined. But what will matter in the longer run is how the technology gets merged into existing city planning objectives, as well as broader thinking about development and land use. That’s the other reason the Eindhoven project is compelling: one of the various parties looking to explore, and influence, the future of construction there is the city itself.
“I was wondering why [construction] was such a traditional sector,” Vice Mayor Yasin Torunoglu reflected. “It has always been the same way of building houses and new buildings.” And that has led to practical and workaday problems. For instance, the Netherlands has a shortage of skilled bricklayers, which seems like a very 20th-century reason for a construction delay. “I was wondering where the [tech] revolution was,” Torunoglu said.
In helping coordinate the partnership behind what is now called Project Milestone, Torunoglu wanted the city to be directly involved in shaping technology’s impact and regulatory implications—not trailing behind and reacting to change created by others, as is so often the case with tech disruption.
Other partners in the effort include the Eindhoven University of Technology and the design firm Houben en Van Mierlo Architecten. The core technology, developed by the university, was used to build the world’s first concrete 3D-printed bridge in 2017. A big mechanical nozzle mounted on a frame squeezes concrete in precise amounts in a programmed pattern—building walls and forms as a 3D printer would, but on a larger scale.
The latest effort will play out over five years and, like 3D printing itself, build up layer by layer. The first house, a one-story, two-bedroom structure, is meant to be ready by next year. It will be built largely in the university’s construction lab, and transported and assembled on site. (Plumbing and wiring are accommodated in the printed designs and finished on site.) The subsequent houses are steadily larger and more ambitious. The team will draw lessons from each construction to shape the next, on everything from building details to coding issues. The final structure will be “printed” on-site.
The designs are striking, idiosyncratic, and almost blobby, with distinct and unpredictable curves. This is a direct result of the 3D-printing process. Designs can be tweaked and modified house by house in a way that allows “true mass customization,” builder van Gurp said: “Every house can have a different look.” Torunoglu, the Eindhoven vice mayor, made a similar point, arguing that the process could “democratize the industry,” offering unprecedented design input to home buyers.
Of course, that’s a long way away. The process is “really interesting and could reduce the cost of housing in a significant way,” says Armando Carbonell, senior fellow and chair of the Department of Planning and Urban Form at the Lincoln Institute of Land Policy. “But that’s a ‘could.’”
If promised improvements materialize, this method would be 40 percent cheaper than standard construction, advocates of the burgeoning industry say. But as significant as that would be, the impact would still vary. In hot markets like New York or San Francisco, the portion of housing costs attributable to land value is two or three times construction costs; this method would be more effective in those cities if it proves possible to build “up,” increasing density. In cooler markets like Cleveland or St. Louis, where construction drives the cost of housing, 3D-printed homes could drastically lower such costs, Carbonell says. This could have an even greater impact in developing-world contexts.
The Eindhoven project is more directed at higher-end buyers, but that could still significantly help establish 3D printing as a viable construction option, because its success or failure depends on actual consumer acceptance. “It’s a challenge to learn from this process,” Eindhoven Vice Mayor Torunoglu said. “We have to collaborate with the market.”
In a good sign for that collaboration, more than 100 people have already signed up as potential renters. That level of interest isn’t something you can manufacture.
Rob Walker (robwalker.net) is a columnist for the Sunday Business section of The New York Times.
Image: Houben en Van Mierlo Architects